Buy Custom Wire Harness Assembly with Advanced Qualities
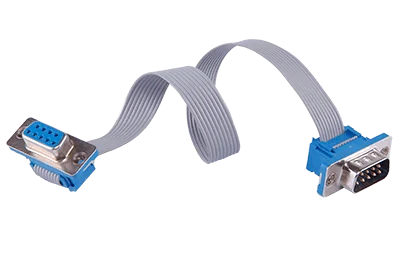
A custom wire Harness assembly is a bundle of wire that has many kinds of cables in it. Because of it the wires stay in a great situation. It will keep the power system always safe and clean. To ensure the flow of the system in the correct direction this is the main part. Each harness can work in tough weather without causing any issues. The custom wire harness assembly is especially made to save space and money. You can get the first-rate harnesses at a fair price easily. Trusted Partner for Custom Solutions Working with skilled custom wire harness manufacturers helps you get parts made for your job and your needs. These pros use top-grade wires, tough covers, and safe ends to make each harness strong and ready for hard work. Each step is checked and tested to ensure it works well and stays secure for cars, machines, boards, and more. Their skill means you get harnesses that last long, work smoothly, and give complete safety in all use cases. They also help plan the right shape and size for your tools and gear, which makes work easy and keeps risks low. Custom OBDII Harness for Vehicles A custom wiring harness for OBDII systems is key for car checks and quick scans. It helps send data fast and clear from the car to the tool with no slowdowns or errors. These harnesses use strong wires, firm ends, and neat layouts to keep the link safe and steady. They are easy to install, check, and use in shops and service spots. They fit old and new cars and can take years of hard daily use in all kinds of weather. This makes them a top pick for car shops that need safe, fast, and precise data links. Key Points: Fast...
Read More »Custom Solutions: a Leading Automotive Wire Harness Supplier
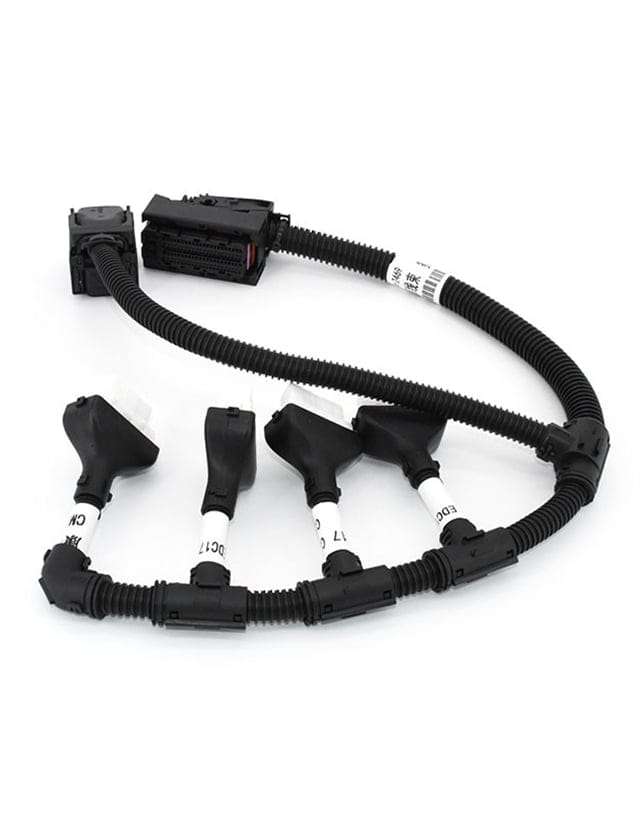
With the better and proper custom wire harness solutions vehicles can smoothly work. An automotive wire harness supplier is the exact way to have the harnesses that fits your vehicle properly. They accurately design the harness to work correctly in the vehicle. You can safely drive the vehicle if you use these harnesses. When making the harnesses the tools that are used are modern and smart. And it helps to Make the best quality harnesses, Why Choose Custom Solutions Custom Solutions is a well-known automotive wire harness supplier. People around the world trust their work. They care a lot about safety. They make strong parts that last a long time. They always bring new and innovative ideas. Each harness is built with care. Each part is made with skill and tested many times. They work with small shops that need just a few parts. They also work with big auto makers that need many. Their harnesses are easy to use. They are safe to use. They check each harness to make sure it fits right and works right. They also give fair prices. Their service is fast, clear, and simple, so anyone can understand it. The Advantages of Custom Work As a custom automotive wire harness manufacturer, the company makes harnesses for every need. They make harnesses for cars that people drive each day. They also make harnesses for heavy trucks. Some harnesses are simple to save money. Some are more complex to handle big systems. Each order is made with care. Every piece is checked again and again. They follow the world auto rules. They meet high safety standards. They make small jobs for special projects. They also make large jobs for big orders. Their wires are strong. Their plugs are safe. Their harnesses can stand heat, cold, and...
Read More »Advanced Automotive Wire Harnesses for Connected Cars
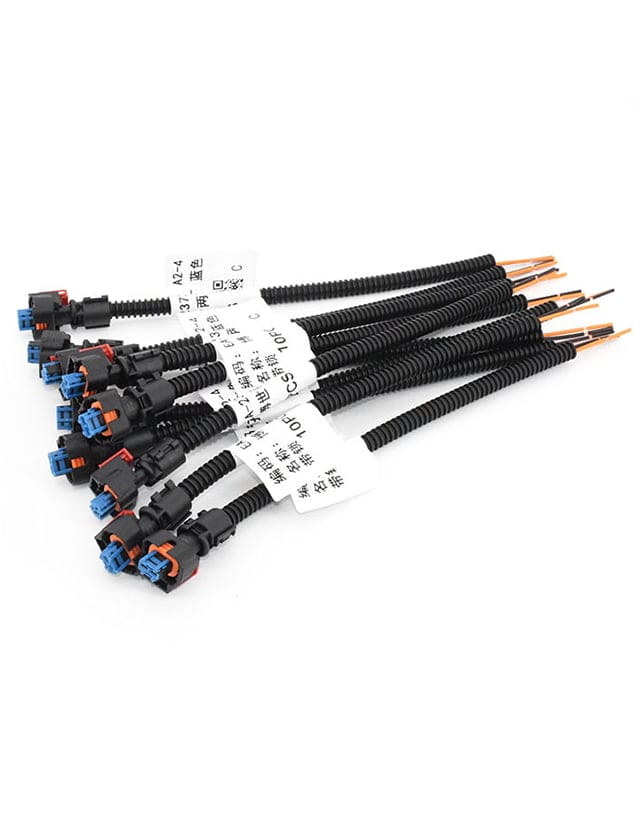
Smart and advanced parts are vital for modern cars. Automotive wire harnesses keep the vehicle engine running smoothly and transfer the signal fastly. These harnesses transfer the exact type of power and signal to the various parts of the cars. With it the cars can be easily updated. The risk level is always low when you use these harnesses in the car for transferring power. To connect the sensors to the vehicle system these are essential parts. Better harness makes the car system more smooth and fast. Why Advanced Harness Systems Matter Modern cars are like moving computers. Many sensors check speed, fuel, heat, and brakes. Each sensor must send signals quickly so the car can react quickly and stay safe. A strong vehicle harness ensures signals travel fast, steady, and with no mistakes. It also helps stop power drops, sparks, and short circuits. This gives drivers safer trips and helps cars last longer on the road. New car wiring kits have better wires, stronger plugs, and safer covers. They can handle more power, heat, and advanced car tech. They also make repairs and upgrades easier and faster for car owners. Without strong automotive wire harnesses, cars may lose control, fail to start, or even break down when you need them most. Benefits of Using Custom Car Harness Extra safety for every part, from small lights to the engine computer. Faster and steadier signals from the ECU to the engine with no delay. Quick and straightforward automotive wire harness repair if a part fails or wears out. Firm hold with automotive wire harness tape and clips that stop wires from moving. Exact fit with a custom automotive wiring harness designed for each car model. Longer life for the car system because wires stay neat, safe, and clean. Lower costs over...
Read More »Custom Wire Harness for Complex Industrial Equipment
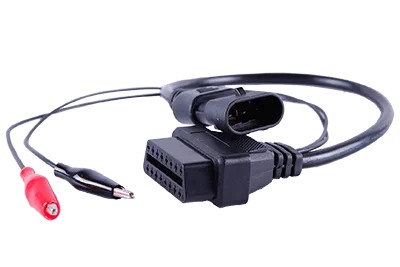
There are reliable parts that are essential for the best performances in the industrial equipment. A custom wire harness is the best way to keep the machine in a great shape. This harness ensures that the machine gets the exact power and signal. For smooth signal and power this harness plays a vital role in the equipment. Each harness is made with proper care to fit the machine perfectly. With a custom made harness you do not need to change the harness every time it saves you both time and money. Power in Every Connection Custom wire harnesses are essential for large and small machines that need power and data to work correctly. They combine power and data in one safe bundle so the machine can run smoothly and powerfully. A custom made wiring harness makes hard work safer and easier because it is made for one machine and not for all. These harnesses last much longer than loose wires that can break quickly. Each wire is cut, shaped, and built with care so no energy is lost and no part is weak. These harnesses help machines work in heat, cold, wet areas, and dusty places without failing. They give peace of mind that the job will be done safely. Choose a Custom Made Wiring Harness Custom wire harness saves a lot of time during setup and repair work. Lowers the risk of mistakes, shorts, or loose links. Keeps all wires neat, tight, and safe at all times. Makes machines last longer and work with fewer problems. Helps workers feel safer and more secure during jobs. Gives more value because it is made for the exact job. A wiring harness custom made is better than wires that are made to fit many things. It is made to match the...
Read More »Future of Automotive Wire Harnesses: Durable Solutions
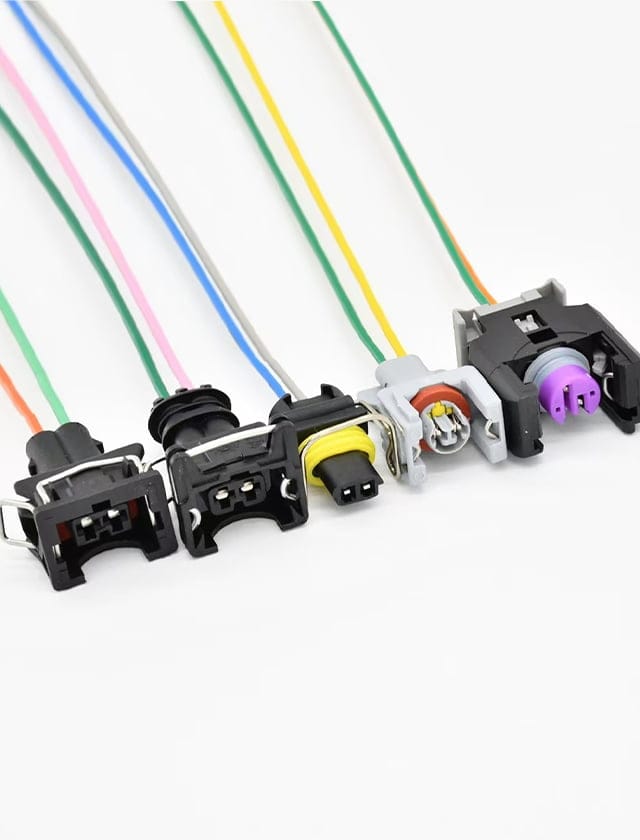
In vehicles, the wire system is essential. In the next generation of vehicles the Automotive wire harnesses will be the most essential part. Vehicles are getting updated with the time so it's vital to keep the harnesses updated and that's why premium quality harnesses are important for a vehicle. A good quality harness offers various kinds of features. These harnesses will offer weather resistances and various types of ports that are durable and flexible. Durable Solutions for Automotive Wire Harnesses Cars, trucks, and big work machines are changing very fast today. The wire harness is an essential part that helps every car and truck work. A wire harness is like the veins in the human body. Just like veins carry blood to every body part, the harness carries power and signals to every part of a vehicle. Without the harness, cars and trucks cannot move, cannot stay safe, and cannot last for a long time. The harness will need to be stronger, lighter, and smarter. This guide will explain the future of automotive wire harness assembly and why durable harnesses will matter even more. It will also share how clips, tape, connectors, kits, and custom harnesses help. Finally, it will explain why QL-Custom Technology Ltd. is one of the best names in the world for strong, safe, and trusted harnesses for cars, trucks, forklifts, and heavy work machines. Automotive Wire Harnesses: Vital Parts of Vehicles Every car has many wires inside it. Wires are in the engine, inside the dashboard, in the doors, and even under the seats. Trucks use even more wires for lights, brakes, GPS, and safety tools. Forklifts, farm machines, and oil rigs also depend on hidden wires. Each wire must be safe and neat. That is why a vehicle harness is needed. The harness keeps the...
Read More »Automotive Wire Harnesses in Advancing IoT Device Integration

Cars today are not just cars. They are smart machines that can share and connect. Modern cars use screens, apps, sensors, and tools to keep people safe and happy. Automotive wire harnesses links all these parts safely and neatly. It lets cars connect to the internet and other devices without problems. It helps signals move fast and precisely. A harness keeps wires safe even in heat, rain, snow, or dust. Without a harness, IoT car devices could lose power or stop working. With a harness, cars stay smart and safe. A harness connects phones, GPS, apps, and safety tools so they work without risk. It ensures the car is ready for driving and smart tech use. Automotive Wire Harnesses in Advancing IoT Automotive wire harnesses are like the primary nerves of a car. They hold many wires together in one strong bundle. They carry power and signals, so each car part works properly. Today's cars are like rolling computers, full of innovative tools. These automotive wire harnesses make sure every sensor and device talks fast and straightforward. They also stop wires from getting too hot, bending, or breaking. Without them, even the smallest car part could stop working. Role of Automotive Wire Harnesses in IoT Vehicles Smart cars use sensors and chips to share data every second. These parts need clean and steady links to work correctly. A wire harness holds wires tight, shields them, and keeps them neat. It stops wires from wearing out and keeps signals strong. It is like a big road carrying power and data, so nothing is lost. Benefits: Signal stays strong with no cuts. Less risk of fire or shorts. Easy to set up and easy to fix. Car parts last longer. Self-driving systems stay steady. Why Choose the Right Wire Harness? Picking the...
Read More »Ensure Custom Wire Harnesses Quality: Vital Testing Methods
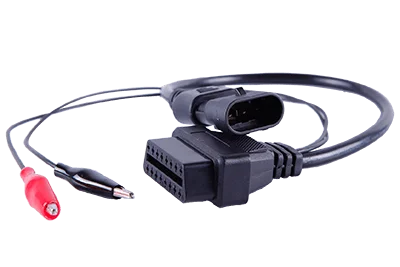
Testing custom wire harnesses is a vital part to ensure the quality. With this process you can find out how reliable the harness materials are. With testing you can find out the issues and prevent them before it gets bigger. With it you can be sure to use it for various tasks daily. If the wires are tested then the power supply will be smooth when you use it. It's vital to check each connection before you use them. The testing process also ensures that the harnesses are ready for rough use. Each test is essential to confirm that the harnesses are ready for every kind of weather. If the testing is skipped then the harness will cost you money and time later. Ensuring Custom Wire Harnesses Quality Custom wire harnesses are key parts in many tools we use each day. They safely move power, signals, and data from one spot to another. A harness is a group of wires tied into one bundle so they do not tangle or break. You can see them in cars, planes, hospital machines, robots, and home tools like washing machines. Without harnesses, wires would hang loose, be hard to fix, and cause danger. When a harness fails, a car may stop, a robot may not move, or even a fire could start. This is why testing is a must. Each wire harness manufacturing company checks every harness to keep users safe, save money, and build trust. Testing shows proof that a harness will work even in hard times. Why Testing Matters in Custom Wire Harness Making Custom wire harness manufacturers make parts that must stay strong for many years. These harnesses face heat, cold, rain, dust, and shaking. Without tests, wires might snap, joints might get loose, or sparks might fly. These risks...
Read More »Design a custom wire harness for a unique project
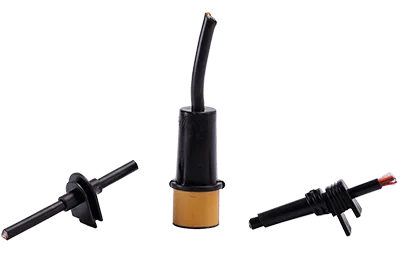
A custom wire harness is exactly made according to the project's needs. These harnesses ensure that the work is done without any issues. It keeps the cables in one place which is vital for neat and clean wires. It keeps the wires safe from outer problems and saves you time. You can easily select the wire as your needs. And because of that you do not need to be worried about picking the wrong wires. These harnesses smoothly pass power and signal. These are vital parts of the control system. Custom Wire Harness for a Vital Project Making a custom wire harness is very important when working on a new project that needs power. A harness is more than just wires. It is a complete system that keeps wires neat, safe, and easy to use. Think of it as a bundle that guides wires in one path. It stops them from tangling. It stops them from breaking. It blocks heat that could burn them. It keeps them safe from sharp parts. A harness makes checking, fixing, or swapping a wire easy. It saves space, saves time, and keeps people safe. It makes any project look clean and pro. It works like a map that helps power travel in the best way. Select a Custom Wire Harness A Custom wire harness supplier makes harnesses that fit the exact job. Every job is unique. A car is not the same as a boat. A robot is not the same as a farm tool. A regular wire may not bend right. It may not fit in a small space. It may break when a machine moves. A custom harness is made to stop these problems. It fits tight spots. It bends around sharp corners. It works in hot, cold, or wet areas....
Read More »Reliable Automotive Wire Harness Suppliers for Production
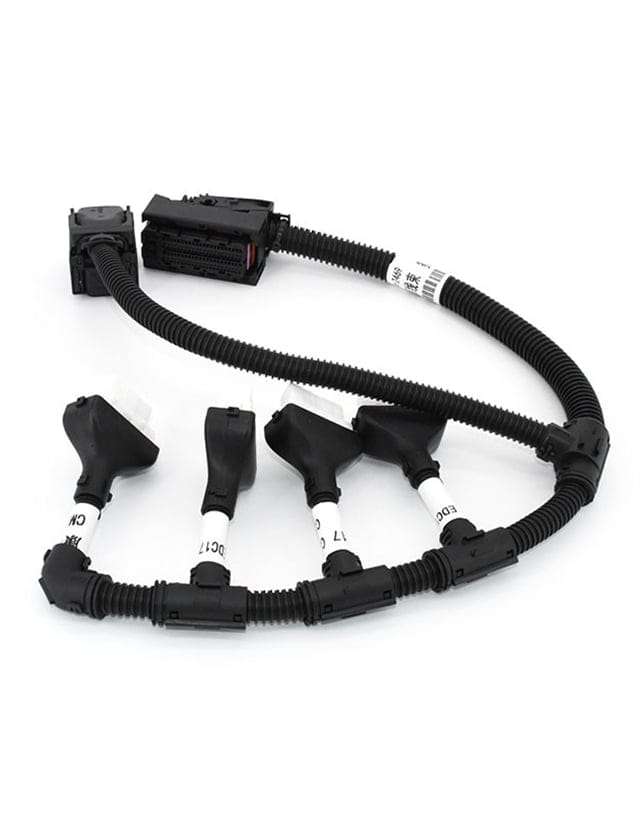
Selecting the right type and reliable automotive wire harness suppliers are vital parts when working with the wire harness. A good quality and trusted seller will always supply you with a harness made with high quality material that will fit your needs exactly. The harness must be tested and the harness should also resist every tough weather. And a reliable supplier will also follow the safety rules to make the harness safe. And if you need the best harness then you need a reliable supplier (QL-Custom Technology Ltd.). Automotive Wire Harness Suppliers for Safe Production Finding reliable automotive wire harness suppliers is essential for building cars, trucks, and heavy machines. A wire harness is like the body’s nerve system. It carries power and signals to every part of the vehicle. Without it, nothing works. If the harness is damaged, the car can stop, jobs can be delayed, money can be lost, and safety can be at risk. In this guide, you will learn about the main types of harnesses, how they help, and why QL-Custom Technology Ltd. is a wise choice. Why High-Quality Wire Harnesses Matters A wire harness connects every electrical part in a vehicle. It powers the engine, lights, sensors, and dashboard. If the harness is weak, power may fail, signals can be wrong, or the system can stop. This can cause high repair costs, long delays, and unhappy customers. Trusted wire harness companies give you: Strong cables that last many years. Safe and steady power flow. Perfect fit for many vehicles. Fewer breakdowns and less downtime. A strong wire harness company uses strict testing to keep your work moving without problems. Selecting the Best Automotive Harness Supplier When choosing reliable automotive wire harness suppliers, look for quality and flexibility: ISO certification for safety and...
Read More »Get Accurate Production: Custom Wire Harness Manufacturers
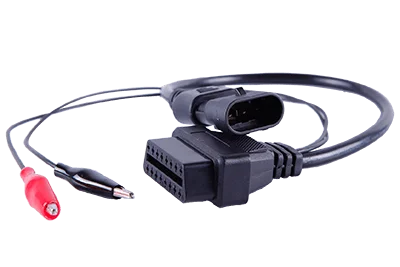
Almost every electric machine needs a wire harness for power and signal supply. Best and the leading custom wire harness manufacturers always use top quality wire harness design and materials for making the harness. They make sure everything is working exactly before delivering it to you by checking the harness. And they always follow the safety rules when building the harness to ensure it will not harm the system. A fine quality harness always makes differences when working on a project. Custom Wire Harness Manufacturers for Top Results Choosing the right custom wire harness manufacturers is a big step when you want safe, strong, and dependable parts. These harnesses affect the safety, strength, and life of your products. Skilled custom wire harness manufacturers take time to plan each step. They pick the best materials, cut wires correctly, and carefully fit each part. They test every wire and cable to ensure it works well before sending it to you. This careful work means your products will last longer, work better, and save you time, stress, and money. Why Skilled Wire Harness Assembly Company Matters A trusted wire harness company uses trained workers, modern tools, and a clear plan to build harnesses correctly. Custom wire harness manufacturers follow safe steps and check quality at every stage. Every task is done with care, from measuring and cutting to adding connectors and final testing. When you get your harness, it will be ready to use, fit well, and work immediately. Benefits of a Skilled Wire Harness Assembly Company: 1- High-quality parts you can count on 2- Fast delivery without late orders 3- Lower risk of product failure 4- Same good quality every time 5- A team that listens to your needs 6- Can make small or big orders Feature Benefit Quality parts...
Read More »