The Wire Cable Harness Drawing Standards
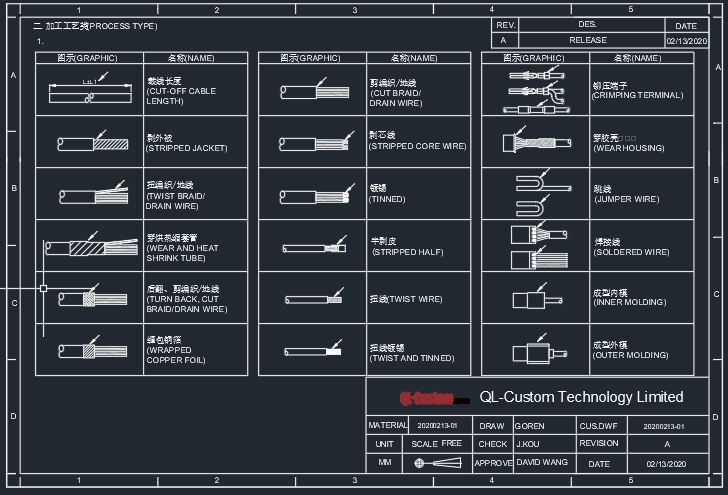
Importance of the Wire and Cable Harness Drawing In the realm of modern engineering and design, wire cable harness drawings hold paramount importance. These drawings serve as blueprints that detail the intricate layouts of wiring systems, ensuring that each component is correctly connected and functioning as intended. Without precise drawings, the likelihood of errors increases, which can lead to system failures, costly repairs, and even hazardous situations. For engineers and designers, mastering wire cable harness drawing standards is not just an option but a necessity to ensure the reliability and safety of their projects. Wire cable harness drawings are essential for several reasons. Firstly, they provide a visual representation of the electrical connections and layout, making it easier for engineers to understand and communicate the design to others involved in the project. This includes manufacturers, technicians, and quality control personnel. A well-drafted harness drawing eliminates ambiguities, reducing the risk of misinterpretation and ensuring that everyone is on the same page. [caption id="attachment_8110" align="alignnone" width="541"] Wire Cable Harness[/caption] Secondly, these drawings play a critical role in the manufacturing process. They guide the assembly of the wire harness, specifying the lengths of wires, the types of connectors, and the routing paths. This level of detail is crucial for ensuring that the harness fits correctly within the physical constraints of the application, whether it's in an automotive, aerospace, or industrial setting. Accurate drawings help streamline the production process, minimize errors, and enhance the overall quality of the final product. Mastering Wire Cable Harness Drawing Standards: A Comprehensive Guide for Engineers and Designers [caption id="attachment_8109" align="alignnone" width="777"] Wire Cable Harness[/caption] To master wire cable harness drawing standards, engineers and designers must familiarize themselves with industry norms and best practices. These standards are established by organizations such as the International Electrotechnical Commission (IEC), the Institute...
Read More »Which Certificates Wire Harness Involved?
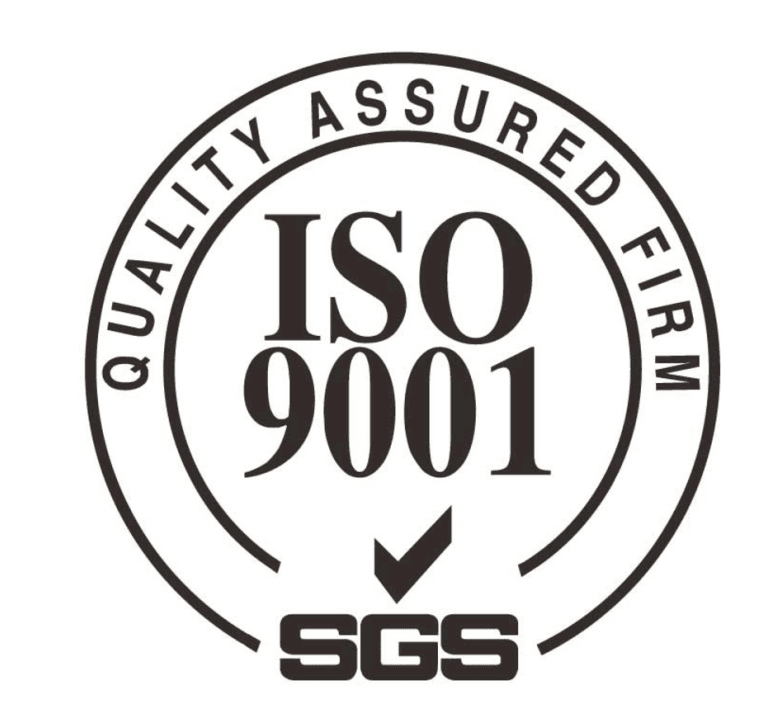
Which Certificates Wire Harness Involved? In the increasingly competitive wire harness market, product certification and factory certification shows particularly important, through the professional testing organizations to carry out strict quality control of product quality, you can effectively screen out qualified products, as well as high-quality suppliers, is a kind of protection for customers. 1- Product Certification RoHS 1. RoHS certification is a mandatory standard developed by the European Union. It is mainly used to regulate the material and process standards of electrical and electronic products, so that it is more conducive to human health and environmental protection. Rohs has been incorporated into the EU mandatory certification CE, generally only require a test report on it, but if the customer needs a certificate, you can also issue a CE certificate. It is mainly for the raw material of the product to be certified. Reach 2-Reach is only a test report, there is no certificate, REACH certification is the EU regulation “Registration, Evaluation, Authorization and Restriction of Legal Goods”. It is mainly for the raw materials of the product to be certified. Water-proof 3-Waterproof certification: First, we need to find out is the customer requirements of the material itself waterproof or design and manufacture of waterproof, which is our priority. About the material itself waterproof: the material itself waterproof means that the connector or wire and cable material can be used outdoors, will not be in the case of immersion in the physical deterioration. Manufacturing design waterproof: It means that after this product is designed and manufactured, this design will not enter water or dust, such as our common strain relief design. UL 4-UL: U.S. Security Laboratory certification, proving that the product meets U.S. safety standards. UL is mainly for North America, out of the U.S. harnesses are...
Read More »The design logic of Coiled Cable

Coil Cable Design, Manufacturing, Length Calculation and Precautions 1. What is a Coiled Cable ? A Coiled cable, also known as a retractable coiled cord or spiral cable, is a type of electrical cable that can stretch and retract like a Coils. The prototype of the coil cable is actually a straight cable. The straight cable is wound around a fixed-size jig rod by winding, and the clamps on both sides are used to clamp the wire. Then it is put into the oven and baked for a certain period of time. It is taken out to form a coil cable. 2. Calculating the Real Length of a Coiled Cable 1. Determine the Structure: Understand the number of coiled sections and straight sections that make up the Coiled cable. 2. Measure the Coil Parameters: Coil length: we need to be clear the coiled part length, from one pc coiled cable L=350mm Coil ID : Measure the coiled part OD=15mm this parameter determines the fixture stick’s OD Coil OD: Measure the coiled part OD=25mm Cable OD: Measure the cable OD5.0mm Then we can work out the cable coiled part how many coils. Use the coiled part length/Wire OD 350/5.0=70coils Counting 1 coil length = πD= 3.14 X (25mm-5.0mm)=62.8mm (‘cause we can’t use the max OD to count the Circumference ) 1 coil 62.8mm X 70 coils = 4396mm+the both ends lengths is the one pc cable real length Note that the measurement method is relatively simple and intuitive but may have some errors. The formula calculation method requires accurate measurement of the structural parameters of the Coiled cable, and the calculated result is only an approximation. In practical calculations, choose the appropriate method based on the specific situation. 4. The Coiled Cable’s straight part orientation on both side The main exit directions of Coiled cables are as follows: I. Straight Exit- ...
Read More »